The Future Is Now: Exploring Next-Generation Technologies in Bottle Injection Molding
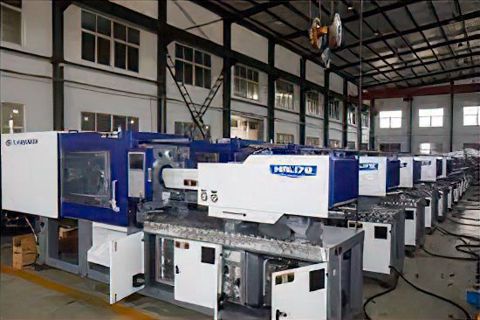
In today's rapidly evolving manufacturing landscape, innovation is key to staying ahead of the competition. One area where significant advancements are being made is in bottle injection molding technology. This article will delve into the latest developments in this field, exploring how next-generation technologies are shaping the future of bottle production.
Introduction to Bottle Injection Molding
Bottle injection molding is a manufacturing process used to produce plastic bottles efficiently and cost-effectively. It involves injecting molten plastic material into a mold cavity, which then cools and solidifies to form the desired shape. This method is widely used in industries such as beverage packaging, cosmetics, and pharmaceuticals due to its versatility and scalability.
Evolution of Injection Molding Technology
Traditionally, injection molding relied on conventional methods that had limitations in terms of speed, precision, and material versatility. However, with the advent of next-generation technologies, such as high-speed injection molding and multi-material injection molding, these constraints have been overcome. Advanced machinery and software have revolutionized the way bottles are manufactured, allowing for greater efficiency and customization.
Next-Generation Technologies in Bottle Injection Molding
High-Speed Injection Molding
High-speed injection molding utilizes state-of-the-art machinery and robotics to achieve faster cycle times and higher production volumes. By optimizing the injection and cooling processes, manufacturers can significantly reduce lead times and increase output without compromising on quality.
Multi-Material Injection Molding
Multi-material injection molding enables the production of bottles with complex designs and functionalities by combining different types of plastics in a single mold. This technology allows for the integration of features such as barriers, seals, and handles, opening up new possibilities for product innovation and differentiation.
In-Mold Labeling (IML) Technology
In-mold labeling (IML) technology integrates labels directly into the molding process, eliminating the need for secondary labeling operations. This results in seamless, durable, and visually appealing packaging solutions that enhance brand image and the consumer experience.
Benefits of Next-Generation Technologies
The adoption of next-generation technologies in bottle injection molding offers several benefits for manufacturers:
Enhanced efficiency and productivity: Faster cycle times and higher throughput rates translate to increased production capacity and reduced time-to-market.
Improved product quality: Advanced machinery and automation ensure consistent quality and precision, minimizing defects and waste.
Cost-effectiveness: Despite initial investment costs, the long-term savings from improved efficiency and reduced scrap make next-gen technologies a financially viable option for manufacturers.
Challenges and Considerations
While next-generation technologies hold great promise, there are certain challenges and considerations that manufacturers need to address:
Initial investment costs: Upgrading to advanced machinery and software requires a significant upfront investment, which may deter some companies from adopting these technologies.
Training requirements: Operators and technicians need to undergo specialized training to operate and maintain next-gen equipment effectively.
Maintenance and troubleshooting: Advanced machinery may require regular maintenance and technical support to ensure optimal performance and uptime.
Case Studies: Success Stories
Several companies have successfully embraced next-generation technologies in bottle injection molding and have achieved remarkable results. From increased production efficiency to enhanced product quality, these success stories demonstrate the transformative impact of innovation in manufacturing.
Future Trends and Innovations
Looking ahead, the future of bottle injection molding is filled with exciting possibilities. Emerging technologies such as 3D printing, nanotechnology, and artificial intelligence are poised to further revolutionize the industry, opening up new avenues for customization, sustainability, and efficiency.
Environmental Sustainability
In addition to driving efficiency and productivity, next-generation technologies also play a crucial role in promoting environmental sustainability. By optimizing material usage, reducing waste, and enabling recyclability, these innovations contribute to a more eco-friendly and socially responsible manufacturing ecosystem.
Conclusion
In conclusion, next-generation technologies are reshaping the landscape of bottle injection molding, offering unprecedented levels of speed, precision, and customization. While challenges remain, the benefits far outweigh the costs, making it imperative for manufacturers to embrace innovation and stay ahead of the curve.
Unique FAQs
How do next-generation technologies improve efficiency in bottle injection molding?
What are the key considerations for manufacturers looking to adopt advanced injection molding technologies?
Can next-gen technologies help reduce the environmental impact of bottle production?
Are there any notable success stories of companies leveraging advanced injection molding techniques?
What does the future hold for innovation in bottle injection molding technology?
0 comments
Be the first to comment!
This post is waiting for your feedback.
Share your thoughts and join the conversation.